Did you know that compressed air generation can amount to over 40% of a plant’s total electricity bill? And that energy consumption can account for over 80% of a compressor’s lifecycle cost? For businesses serious about increasing their profits, energy consumption is an obvious target. It was therefore one of the leading design priorities for our ZT 30-50 VSD⁺ compressors.
Efficiency
Designed for efficiency
Over 80% of a compressor’s lifecycle cost is taken up by the energy it consumes. Moreover, the generation of compressed air can account for more than 40% of a plant’s total electricity bill. The ZR 75-160 VSD+ is not only designed for reliability, but also for efficiency. Our unique and patented elements are designed in-house for maximum efficiency. The superior rotor coating, compact rotor profiles and cooling jackets guarantee maximum compression efficiency. The unique Z seal design guarantees efficient and 100% certified oil-free air for your application.
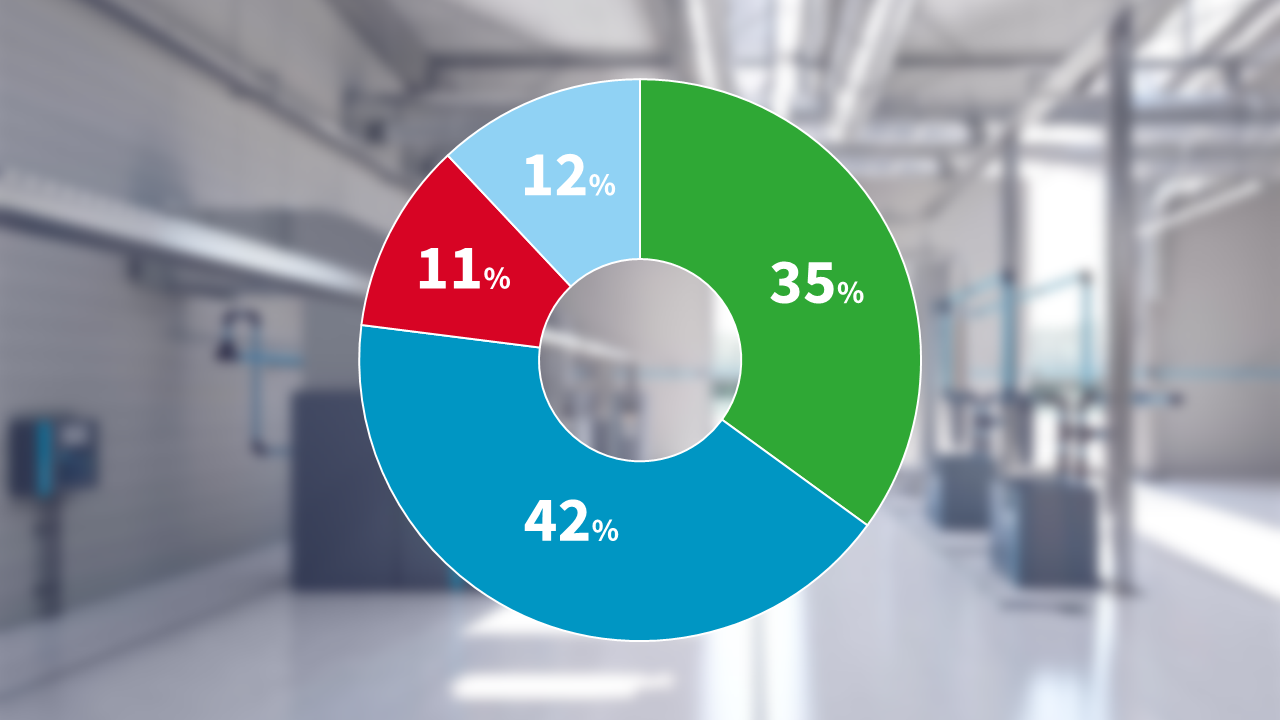
35% = VSD Savings
42% = Energy cost
12% = Installation cost
11% = Maintenance
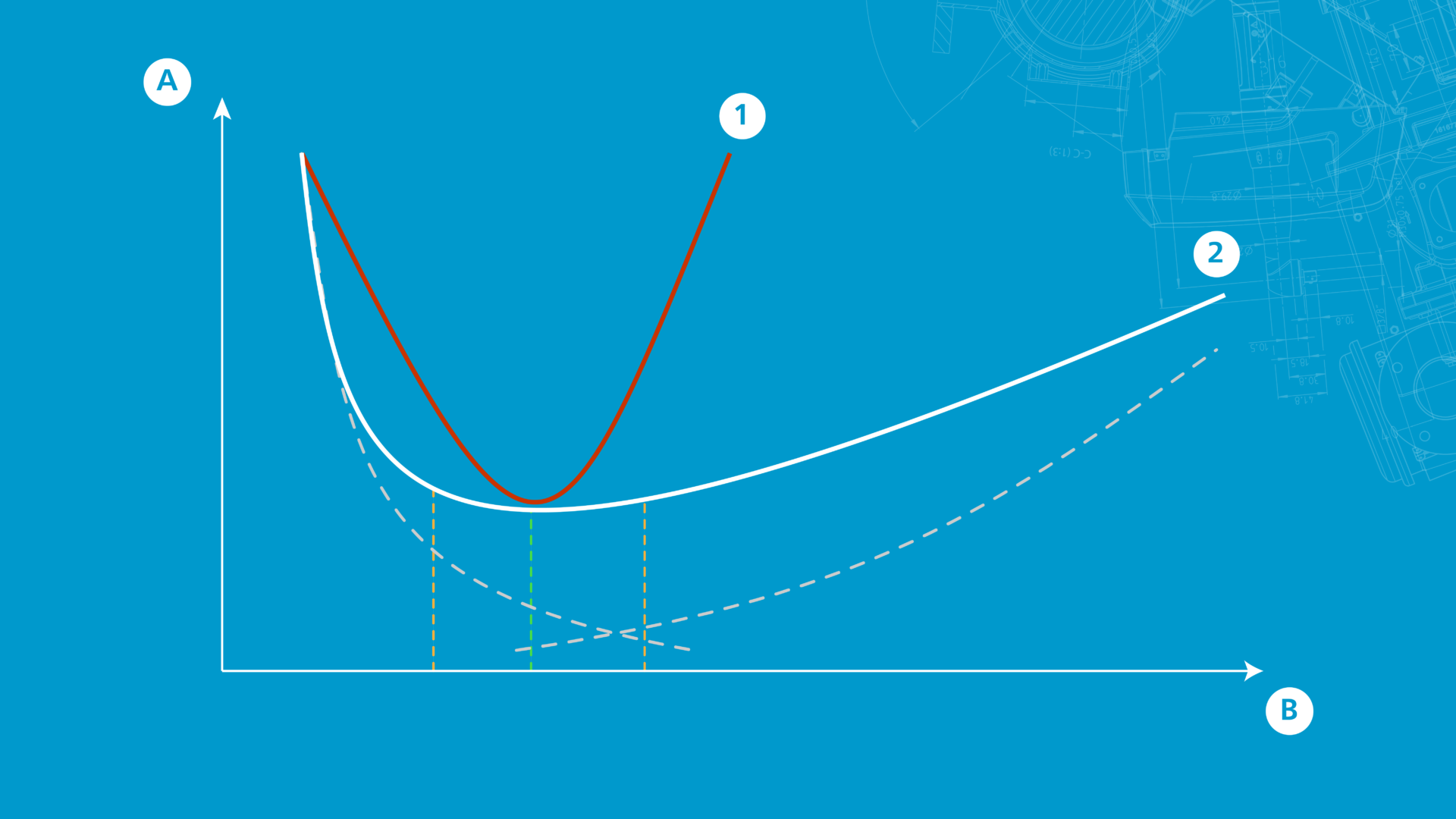
A= Losses
B = Speed
1 = Total losses traditional element
2 = Total losses AC element
VSD⁺ with dual NEOS drives
Atlas Copco pioneered VSD technology in the compressed air industry to offer major energy savings while protecting the environment for future generations. Today, we offer the widest range of integrated VSD compressors on the market.
VSD technology automatically adjusts the motor speed to air demand, reducing energy consumption by up to 35%. For the ZT 75-160 VSD⁺ range, we added a specially designed NEOS inverter to constantly optimize the motor speed, and our own Permanent Magnet Motor for class-leading efficiency.
Featuring dual NEOS drives, the ZT 75-160 VSD⁺ range has the widest operating range on the market. The units can operate from 28 to 100% load without wasting energy from unloaded operation, resulting in huge energy savings during periods of low to medium air demand. The dual NEOS drive system also keeps the compressor working at optimal efficiency – at any pressure – consuming less energy than a standard fixed speed machine or a VSD machine with a fixed gear ratio.
Optimized air flow in the machine
The ZR 75-160 VSD+ brings cool dense air into the package for optimal compression efficiency. The piping and components are strategically placed to minimize the pressure drop in the package, leading to optimal efficiency. The coolers have been
carefully designed to keep the pressure drop at a bare minimum. Our zero loss drains account for zero waste of compressed air, making the ZR 75-160 VSD+ the most efficient machine on the market.
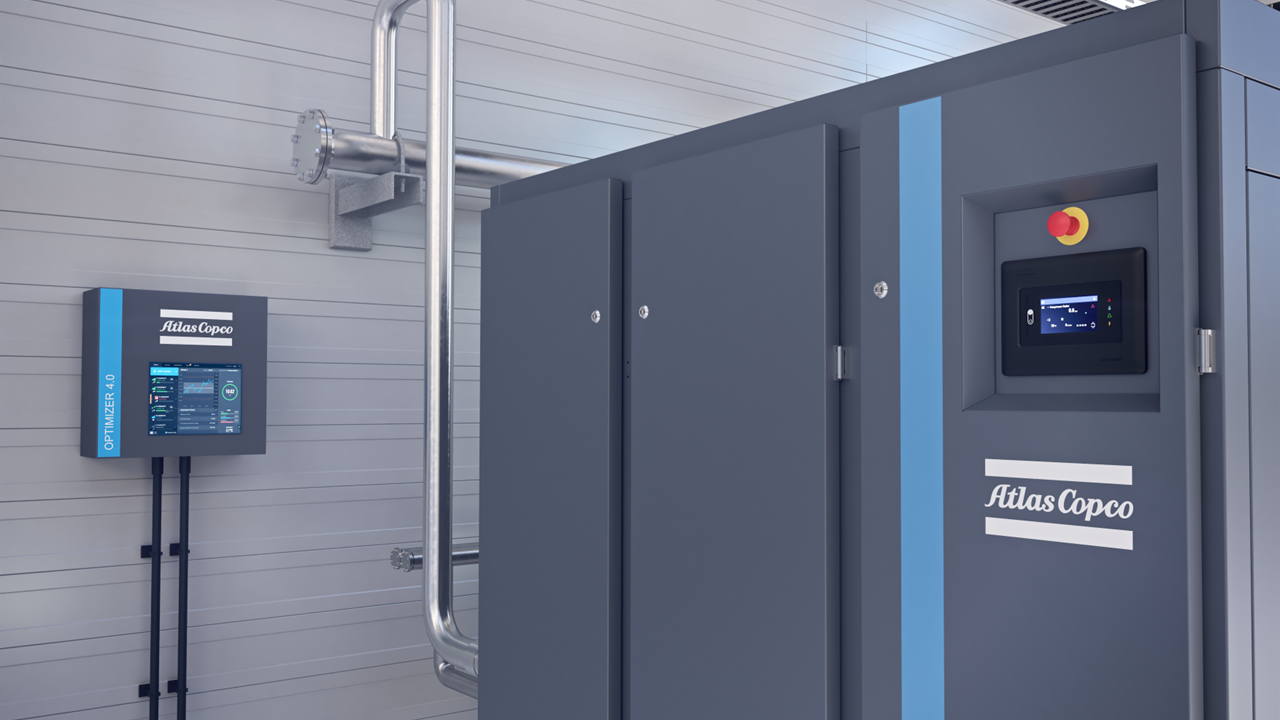
Elektronikon Mk5 Touch
Our Elektronikon Mk5 touch unit controller is designed with Atlas Copco energy efficient algorithms to maximize flow and minimize power consumption. It controls both the compressor and the integrated converter, ensuring maximum machine safety within parameters.
Most production processes create fluctuating levels of demand which can create energy waste in low use periods. Using the Elektronikon® unit
controller, you can switch between two different setpoints to optimize energy use and reduce costs at low use times.
Energy Recovery
You can turn your compressor into an energy source. Air compressors equipped with Energy Recovery can help you achieve your goals in becoming carbon neutral. Compressed air is one of the most important utilities for the industry. It is also one of the largest consumers of energy. Up to 94% of the electrical energy is converted into compression heat. Without energy recovery, this heat is lost into the atmosphere via the cooling system and radiation.
You can use hot water recovered from the compressed air system for sanitary purposes and space heating. But it is particularly suitable for process applications. Using the hot water as boiler pre-feed or directly in processes requiring 70 to 90°C can save you costly energy sources such as natural gas and heating oil.
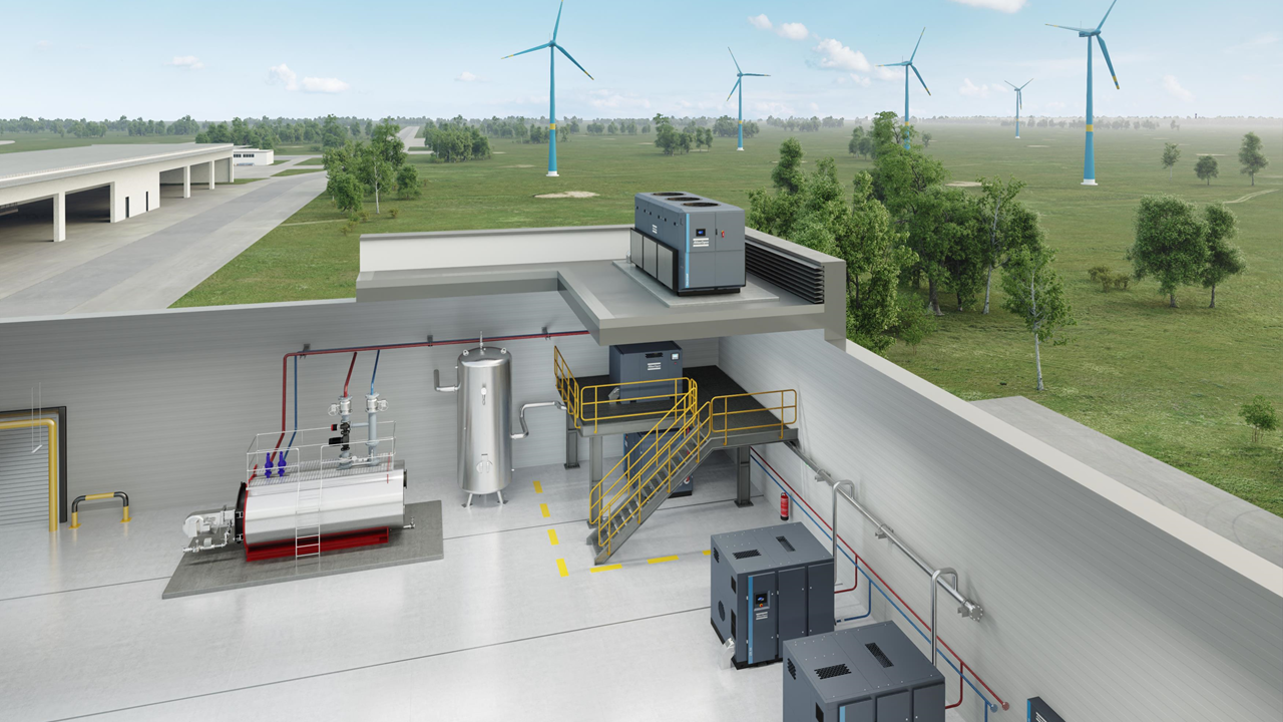
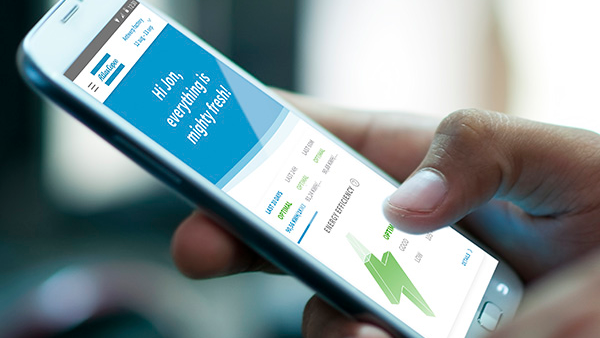
SMARTLINK
Monitor your compressed air installation with SMARTLINK
Knowing the status of your compressed air equipment at all times is the surest way to achieve optimal efficiency and maximum availability.
Go for energy efficiency
Customized reports on the energy efficiency of your compressor room.
Increase uptime
All components are replaced on time, ensuring maximum uptime.
Save money
Early warnings avoid breakdowns and production loss.