In an optimal compressed air and blower installation, the machines are managed in centralized way, resulting in the highest overall efficiency.
Save energy through smart controls
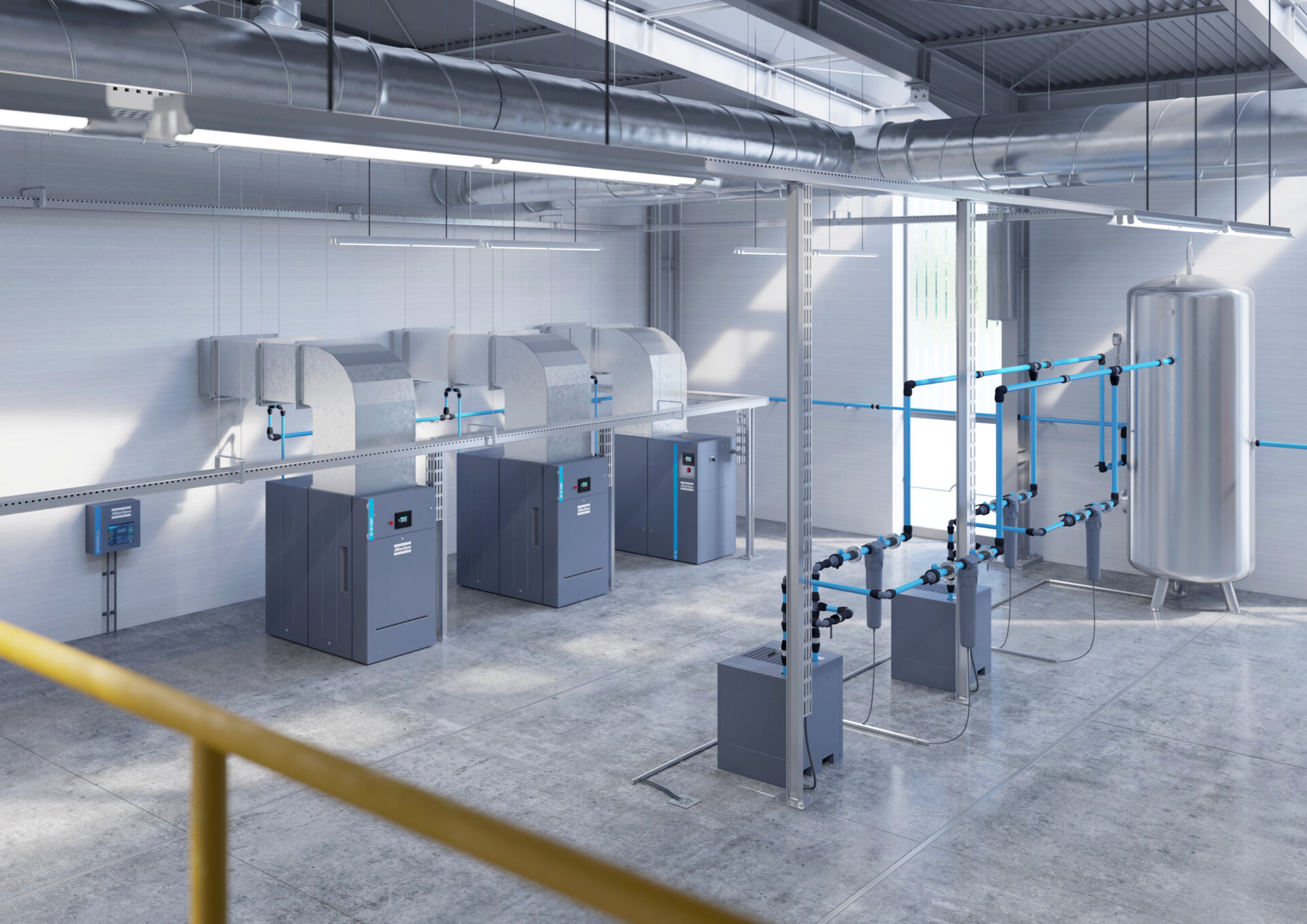
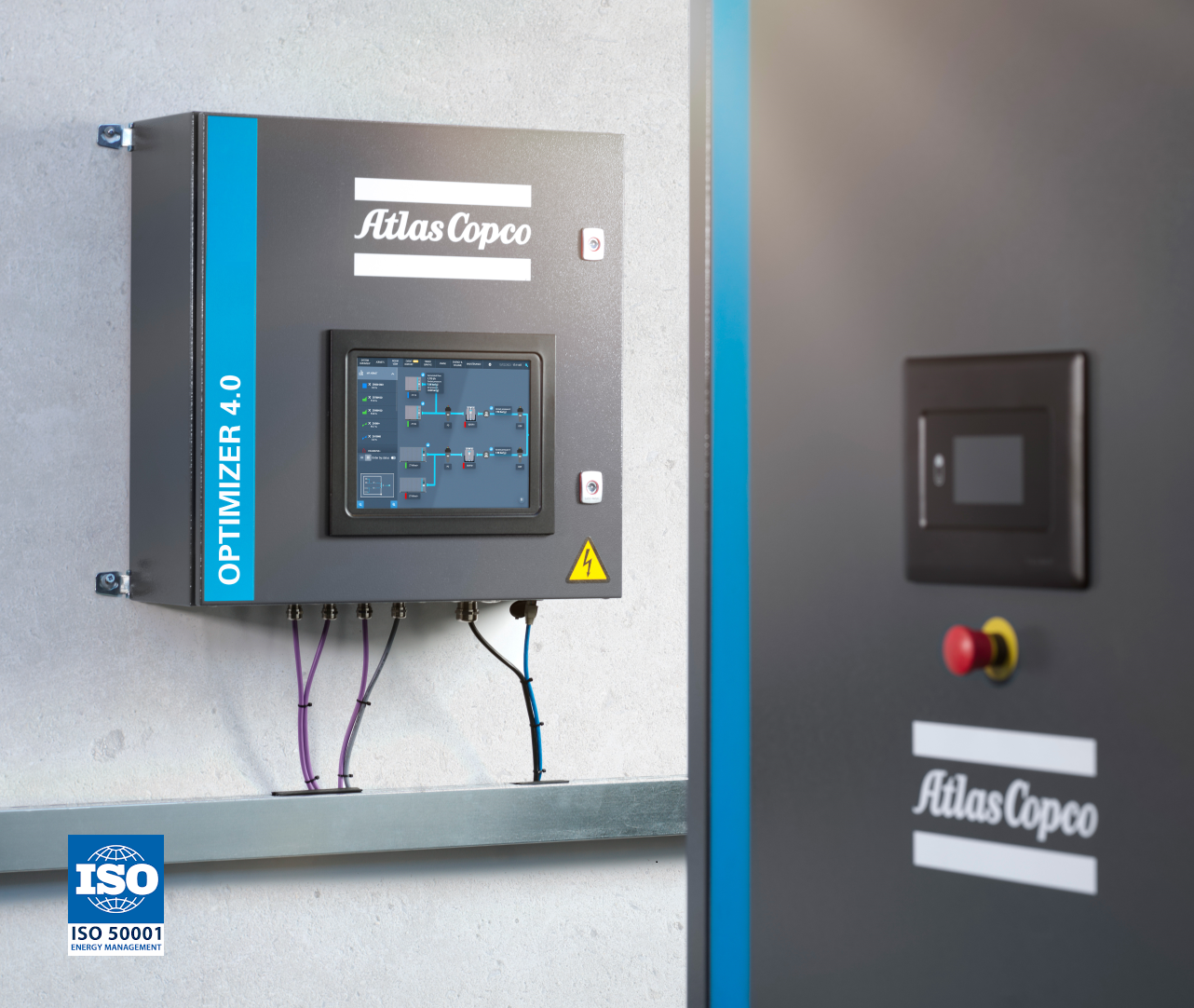
1. Energy Management System
Both the Optimizer 4.0 and the Equalizer 4.0 PRO are ISO50001 compliant as a central energy and maintenance management system. Smart central controllers can efficiently regulate all connected machines, to reduce the energy consumption as much as possible.
The Optimizer 4.0 and Equalizer 4.0 PRO are connected via a communication system with all the different machines, exactly knowing all their operating points in real-time.
The VSD machines operate in their sweet spots and fixed speed machines reduce their unload time as much as possible, resulting in the highest possible efficiency for the overall installation.
With a central controller, a much smaller pressure band can be achieved, resulting in much higher energy savings.
An ISO50001 compliant Energy Management System will lower your production cost significantly and achieve the lowest Total Cost of Ownership!
2. Setpoint control
Applications controlled by a pressure or flow setpoint can easily be integrated in the Optimizer 4.0. As the Equalizer 4.0 PRO is a sequencer, it is equipped with pressure control.
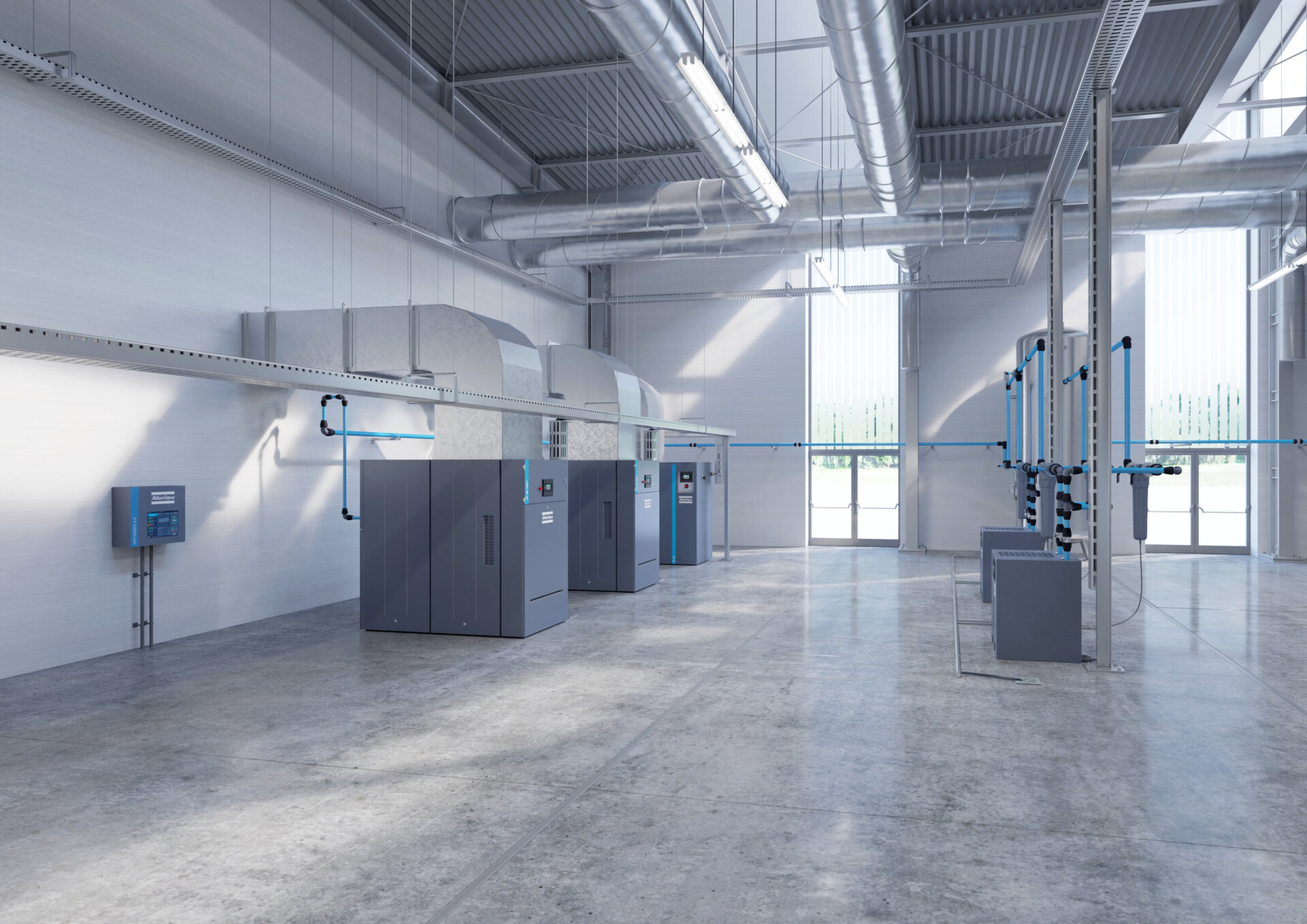
Pressure control
Compared to local control, where the individual pressure setpoints are set to assure cascading, the use of a central controller allows for a much smaller pressure band. Having a central controller results in lower pressure fluctuations and a much more stable output pressure to your application.
A more narrow and combined pressure band also results in a lower operating pressure for the individual machines:
By reducing the pressure by 1 bar(g) (or 14.5 psi), your energy usage lowers by 7%.
By reducing the pressure by 1 bar(g) (or 14.5 psi), air leakages are decreased by 13%.
Easily switchable pre-programmed pressure bands.
Flow control
Often applications also require a variable flow setpoint, such as aeration, fermentation, … The Optimizer 4.0 is capable of handling multiple compressors and blowers in variable and constant flow control.
Embedded flow bands ensure that the flow is always within the demand, reducing the energy cost related to excess air flow.
The fluctuation of the air flow is minimized as much as possible, even during a sudden change in demand.
The usage of your VSD or centrifugal compressors or blowers is optimized.
3. Control modes
Depending on the desired regulation, the Optimizer 4.0 can be configured with different control modes. These modes can also be combined into a group of compressors & blowers, which is called group management.
Equal wear mode
This mode equalizes the running hours over the machines according to your requirements. The compressors and blowers will equally wear over-time.
Reduces maintenance interventions to one single visit for all your machines.
Planning & administration are more manageable.
Energy Savings mode
In the Energy Savings mode reaching the highest potential energy savings is the main focus, this while assuring a stable pressure output.
The Load – Unload machines are operated in such a way that the unload time is reduced as much as possible.
VSD machines will be regulated to operate in the sweet spot of their performance curves.
Centrifugal machines will work in harmony with the other technologies, avoiding blow-off excess air as much as possible.
Forced sequence mode
Forced Sequence mode gives the full flexibility to select the order in which the compressors or blowers need to be enabled and controlled.
Easily select the sequencing order.
Have the full flexibility on how the machines are controlled.
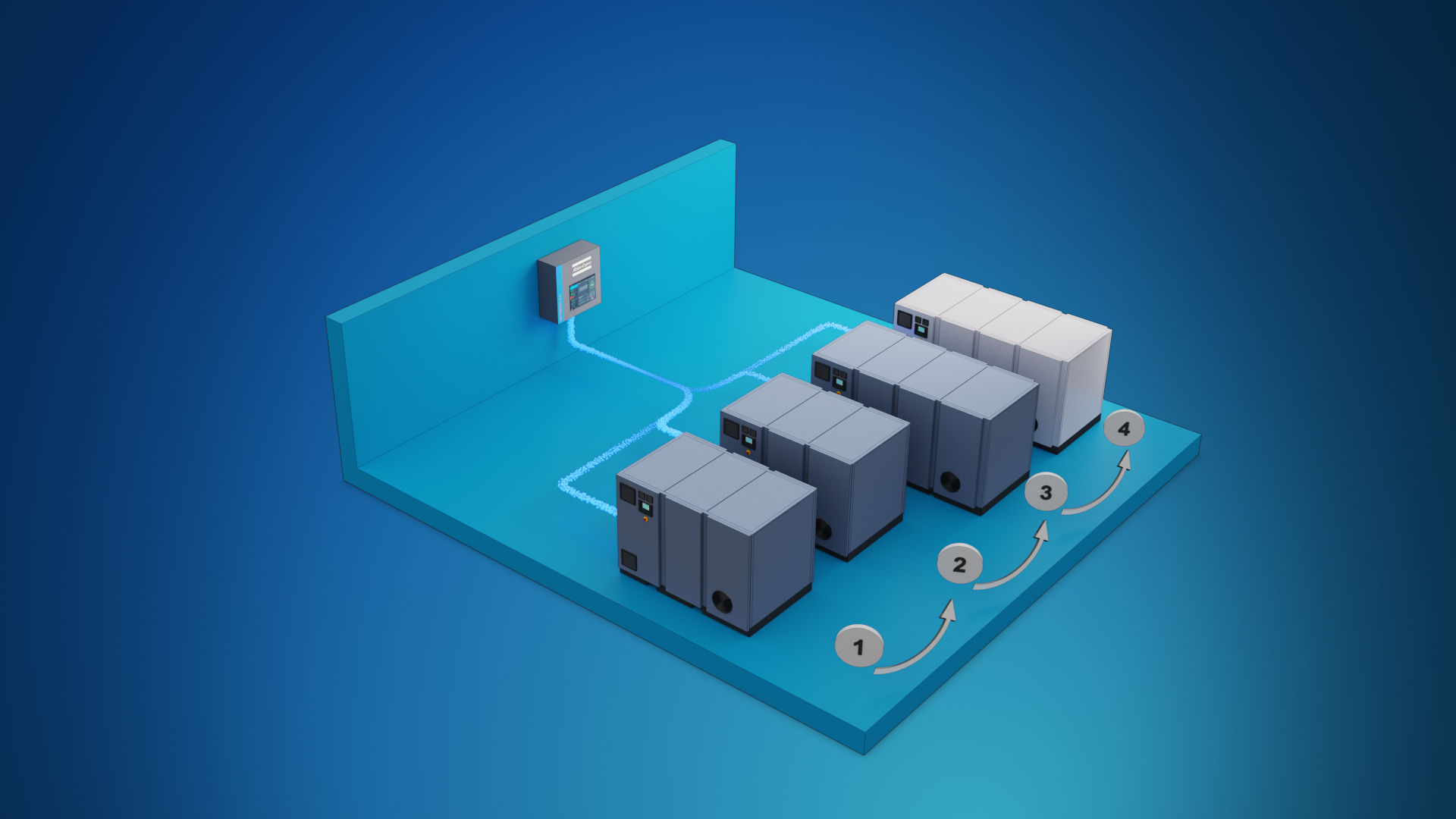
4. There is even much more
Our ISO50001 central controllers have much more capabilities ensuring that your compressed air network is operating according to your requirements: Highest efficiency, improved uptime and an impressive stable pressure output. Maximize your energy saving potential even with non-Atlas Copco machines.
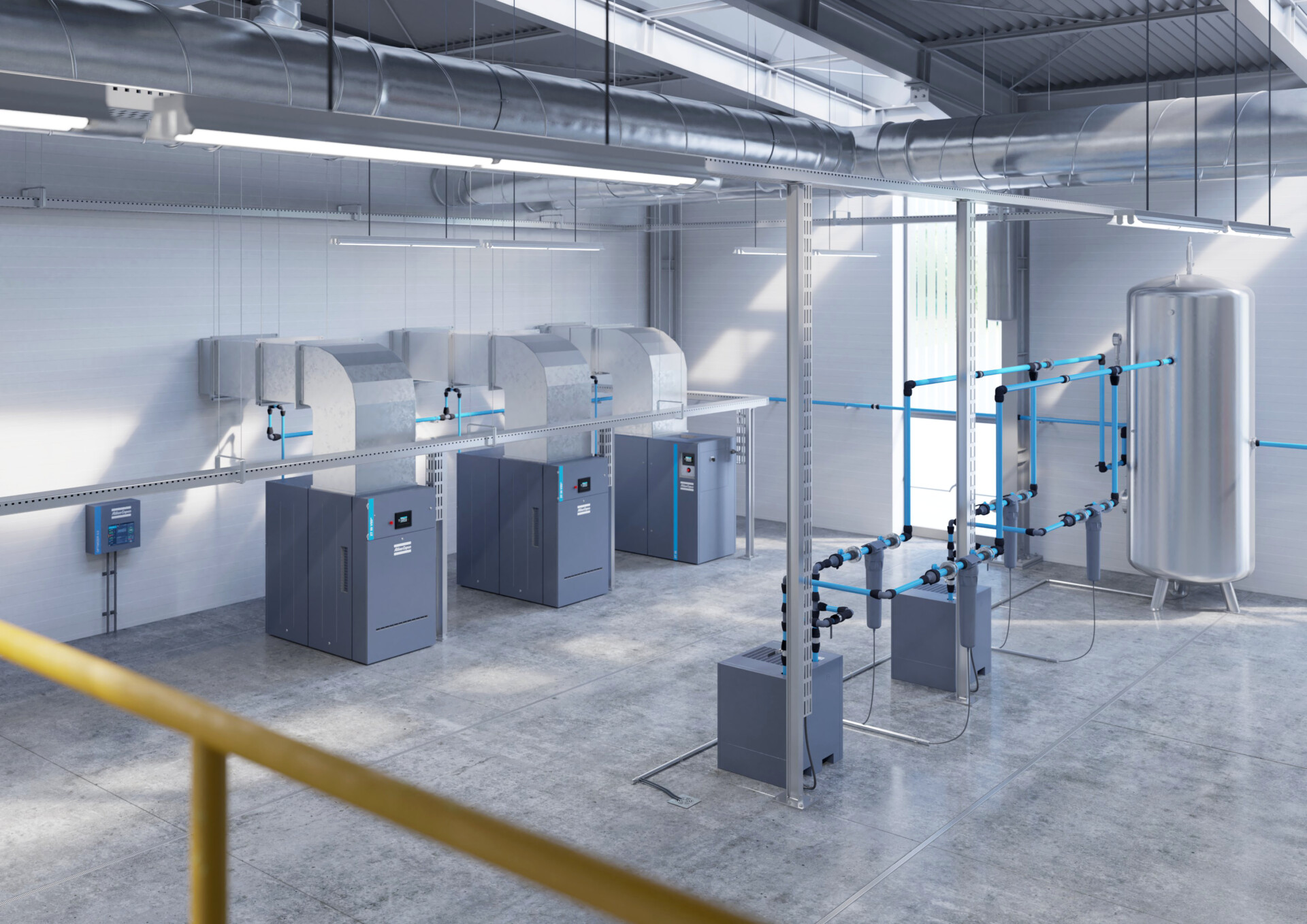