Did you know that compressed air generation can amount to over 40% of a plant’s total electricity bill? And that energy consumption can account for over 80% of a compressor’s lifecycle cost? For businesses serious about increasing their profits, energy consumption is an obvious target. It was therefore one of the leading design priorities for our ZT 30-50 VSD⁺ compressors.
Building energy savings into your process
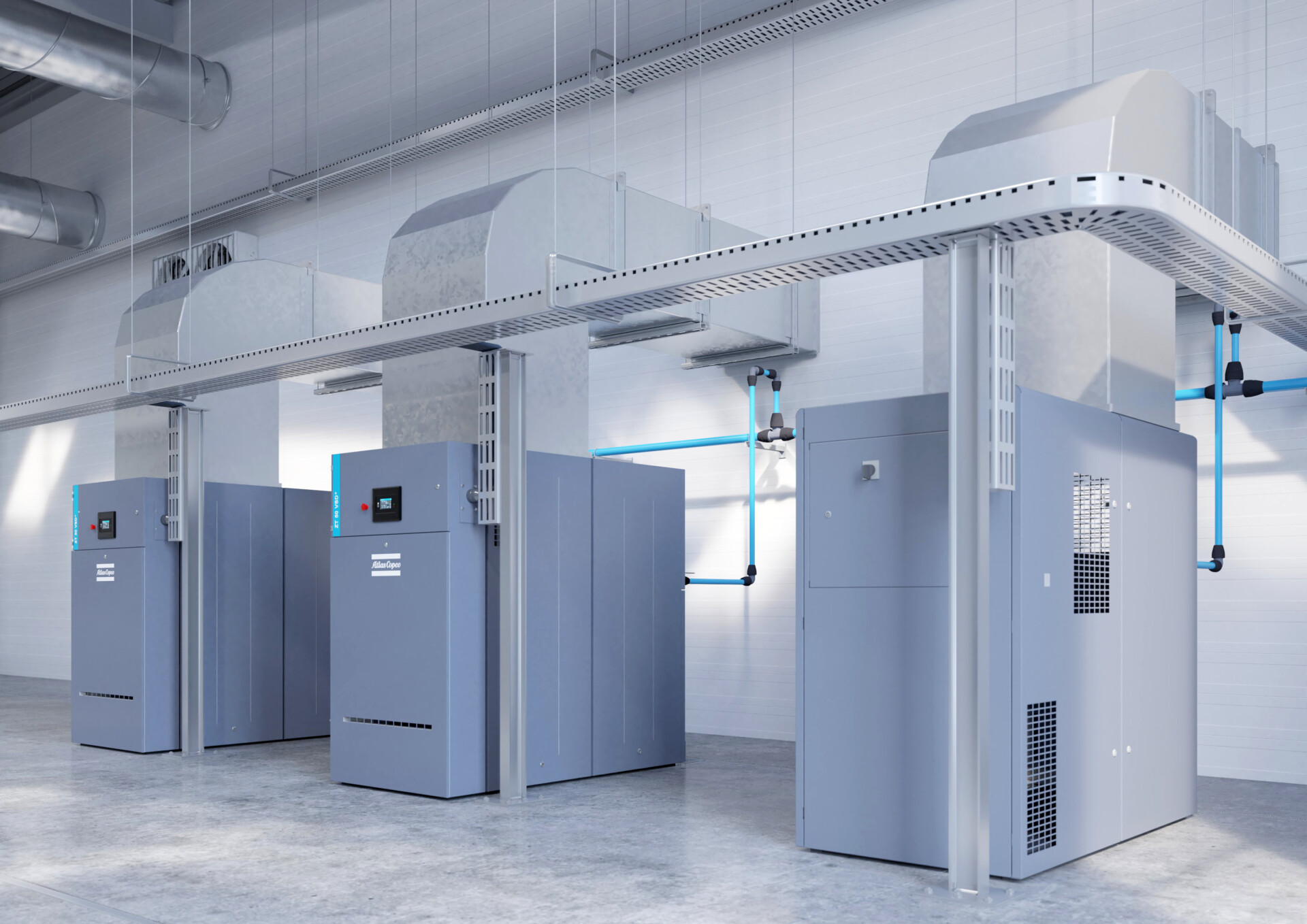
Energy-saving componentsOur engineers took every opportunity to reduce energy consumption in these machines. The patented elements are designed in-house for maximum efficiency. A superior coating on the active surfaces of the stainless steel rotors contributes to the most efficient oil-free tooth technology in this capacity range. A unique Z seal design further reduces running costs and guarantees 100% certified oil-free air for your application. ![]() Element– In-house designed. ![]() Motor– IP66 oil-cooled Permanent Magnet Motor with oil-lubricated bearings. ![]() Neos Next– Exceptional piece of engineering, developed in-house. ![]() VSD cooling fansThe completely redesigned cooling air flow supported by a VSD cooling fan ensures maximum energy savings at lower RPMs. ![]() Plug & play– Integrated rotary drum dryer option (iMD) for moisture sensitive applications. |
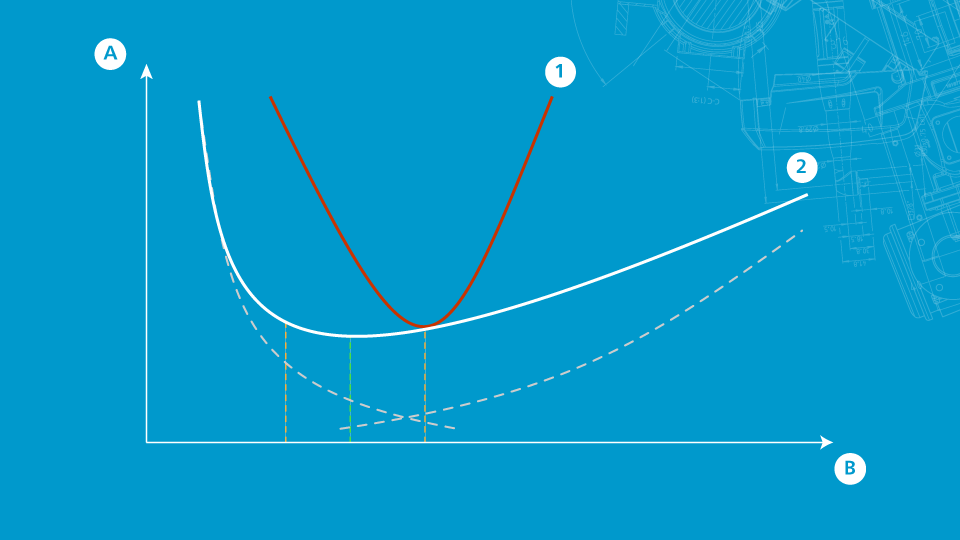
A= Losses
B = Speed
1 = Total losses traditional element
2 = Total losses AC element
VSD⁺ with dual NEOS drives
Atlas Copco pioneered VSD technology in the compressed air industry to offer major energy savings while protecting the environment for future generations. Today, we offer the widest range of integrated VSD compressors on the market.
VSD technology automatically adjusts the motor speed to air demand, reducing energy consumption by up to 35%. For the ZT 30-50 VSD⁺ range, we added a specially designed NEOS inverter to constantly optimize the motor speed, and our own Permanent Magnet Motor for class-leading efficiency.
Featuring dual NEOS drives, the ZT 30-50 VSD⁺ range has the widest operating range on the market. The units can operate from 28 to 100% load without wasting energy from unloaded operation, resulting in huge energy savings during periods of low to medium air demand. The dual NEOS drive system also keeps the compressor working at optimal efficiency – at any pressure – consuming less energy than a standard fixed speed machine or a VSD machine with a fixed gear ratio.
Optimized air flow
The ZT VSD⁺ brings cool, dense air into the package for optimal compression efficiency. Carefully designed coolers and strategically positioned piping and components minimize pressure drop in the package, while zero-loss drains ensure that no compressed air is wasted.
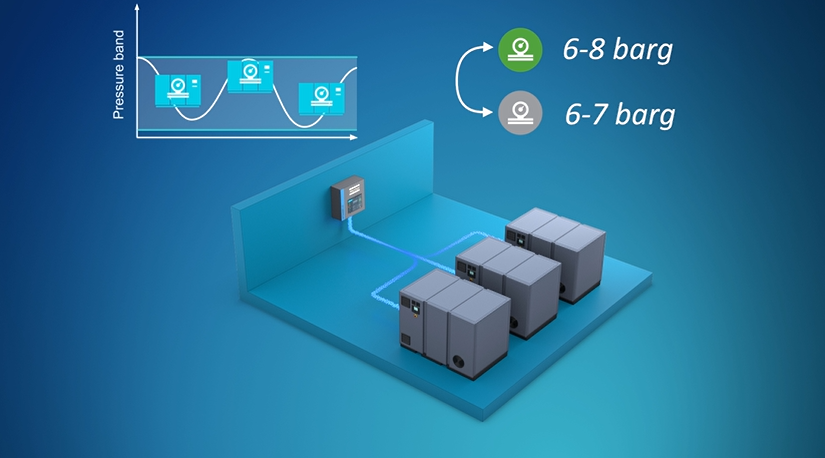
Advanced control algorithms
Advanced algorithms control your equipment to save energy when demand is low. For example, timer functions can stop your machines at night and during the weekend if no compressed air is needed. Alternatively, a dual pressure band can be implemented with lower pressure settings for these periods.